The Sustainable Urban Jungle
New AI-supported concrete buildings could turn cities into carbon sinks like forests.
Construction is one of the major contributors to CO2 emissions. Within that category, one of the biggest CO2 culprits is cement, which is one of the elements of concrete. Worldwide, cement and concrete production generates close to one tenth of all human CO2 emissions. To make cement, limestone is calcinated (its temperature raised without melting it), which releases large amounts of CO2 in a chemical reaction, and the heating of the cement kilns to approximately 1,500 degrees Celsius does the rest. To get an idea of the dimensions, every ton of cement is responsible for about a ton of CO2. So it’s worth thinking about new technologies that aim to decarbonize cement production. Two Berlin startups are determined to make important contributions.
In The Mix
ecoLocked has been pursuing the development of additives for the production of climate-positive concrete since 2021. Climate-positive means not only that there is no CO2 emitted during production, but that CO2 is actually captured overall. Founded by Mario Schmitt, Micheil Gordon and Steff Gerhart, ecoLocked uses biochar, carbon captured in a thermal decomposition method from plant matter. Biochar is the black residue of carbon and ashes which remains after the pyrolysis of waste biomass. Pyrolysis involves the heating of the organic material at high temperatures, a process which moreover creates an energy-rich synthetic gas which can be used as fuel. What remains is a form of charcoal. If you’ve ever caramelized onions or burnt a pizza, you’ve seen stages of pyrolysis, though on an industrial scale it is done without oxygen.
ecoLocked’s process uses biochars made from different biogenic waste matter, for example residue from forestry, sawmills, or food production. These organic materials derive from plants and have previously absorbed CO2 from the atmosphere through photosynthesis. Under normal circumstances, this waste would have reacted to CO2 or methane by being incinerated or left in landfills.
ecoLocked’s functionalized biochar-based additives and admixes can partially replace conventional concrete ingredients such as cement or sand while maintaining the concrete’s strength and workability. The trapped carbon compensates for the CO₂ emissions generated during concrete production, says co-founder and CEO Mario Schmitt, which makes the concrete climate-neutral. “We don’t see it as a substitute for decarbonising concrete, but as a way for the construction industry to take climate action by financing local carbon removal and thereby compensating unabated Scope 3 emissions, such as from cement,” Schmitt emphasizes.
Through ecoLocked’s process, raw biochars are turned into CO2-negative admixes, which can be added to concrete either where it is produced in the factory or on the construction site. Along with the material, ecoLocked’s customers get an optimized recipe to ensure the desired concrete performance. The result is concrete which approaches carbon-neutrality and even has improved functional properties such as less weight and greater stability.
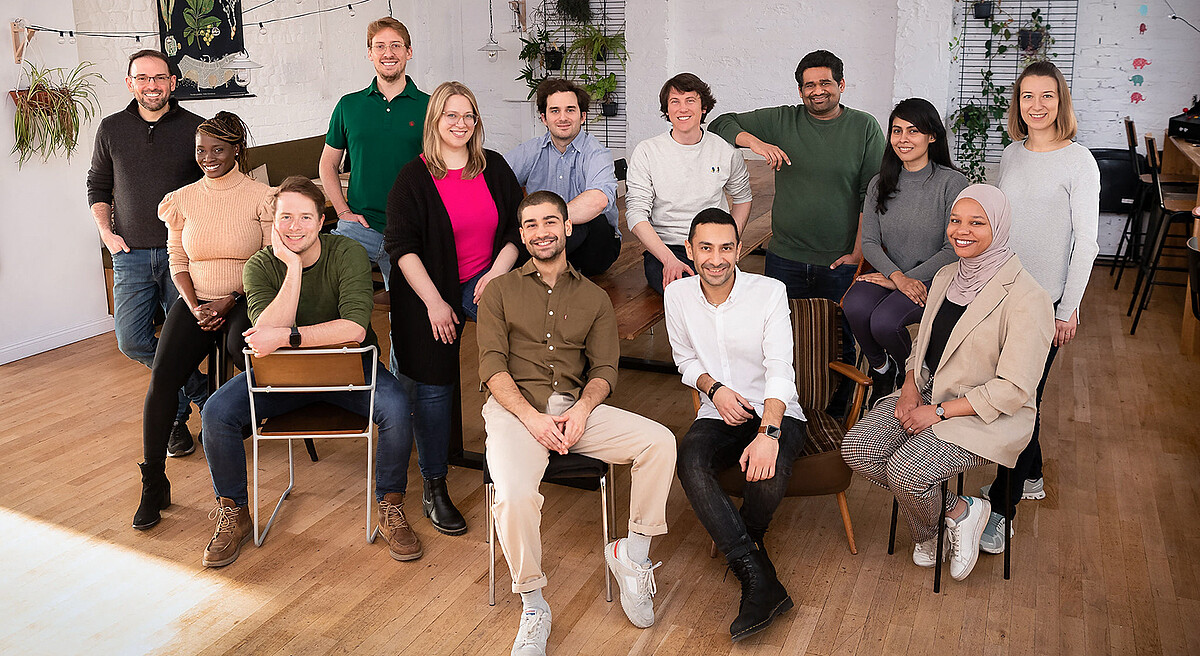
“We want to transform buildings and infrastructure into the largest non-natural carbon sink in the world,” explains ecoLocked Chief Commercial Officer and co-founder Steff Gerhart. Carbon sinks such as forests or the ocean absorb carbon dioxide from the atmosphere. ecoLocked’s vision is the city as a carbon sink, the sustainable urban jungle.
“By reducing cement and trapping carbon, we can improve the carbon footprint of concrete by up to 120 percent,” Gerhart continues. “In addition, we can develop recipes that make the concrete more insulating, lighter, or more durable than conventional concrete.”
ecoLocked is already on the market. “Many carbon removal technologies will still need 10 to 15 years to reach commercial scale. Biochar is a promising technology that can be used now,” says Steff Gerhart. And indeed ecoLocked is already working with concrete manufacturers, such as BNB in Berlin Babelsberg.
Concrete Use-Case Cements AI
Concrete is responsible for 8% of the global emissions, making the industry one of the most CO2 intensive ones worldwide. The main driver for those emissions is cement clinker, a product that results from burning limestone. Limestone contains up to 50% CO2, which evaporates into the atmosphere during the production process of cement clinker. Because of its essential properties, clinker is a main ingredient in today's cement and concrete recipes. The problem is, the higher the amount of clinker in the recipe, the higher the CO2 footprint. An efficient way to reduce these emissions is by reducing the amount of clinker, which can be achieved by substituting it with sustainable alternatives like calcinated clay and limestone powder. However, this leads to a more sensitive concrete product that is hard to realize with manual workflows.
The Berlin-based green-tech startup alcemy provides a software solution tackling this challenge. Founded in 2018 by Leopold Spenner and Dr. Robert Meyer, alcemy uses machine learning and control technology to predict the quality and properties of cement and concrete and enables companies in the cement and concrete industry to optimize quality and production costs while reducing CO2 emissions.
Existing data from production in the cement and concrete plant is analyzed constantly, resulting in quality predictions and optimal setting suggestions for employees. This gives manufacturers the digital tools they need to produce low-CO2 cements and concretes in a more automated, less labor-intensive, more transparent and more cost-effective way.
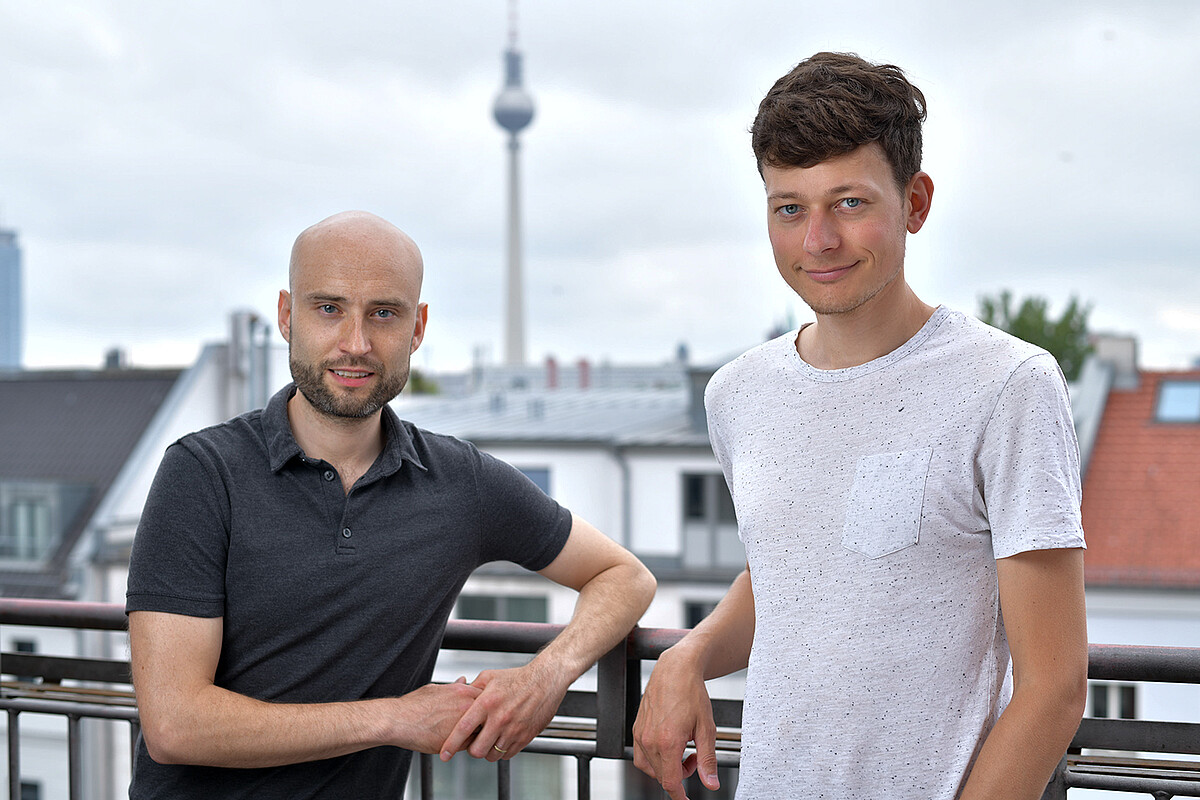
“Our predictive software makes the production of climate-friendly concrete much easier, the product is manufactured more consistently, conserving resources and reducing long-term costs,” says alcemy’s key account manager Tobias Linden. “Our customers can focus more on the issue of decarbonisation without having to compromise on quality.”
The easy-to-implement software solutions enable producers to avoid up to 50% of CO2 emissions, accelerating the decarbonization of cement and concrete internationally, with the goal of saving 100 million tons of CO2 every year from 2030. As of today, one third of all cement producers in Germany are using alcemy’s products and the company has expanded into six other countries.
Building Transformation
Both alcemy and ecoLocked are Berlin “greentechs” that want to transform the construction industry, supporting the transition to climate-neutrality. Taken together, they turn a manually processed raw material into a data-based high-tech product.
With half the world population living in cities, the hope is that the combination of individual solutions can make the entire value chain of construction and building management more sustainable, helping to make Berlin and urbanity all over the world climate-friendly.
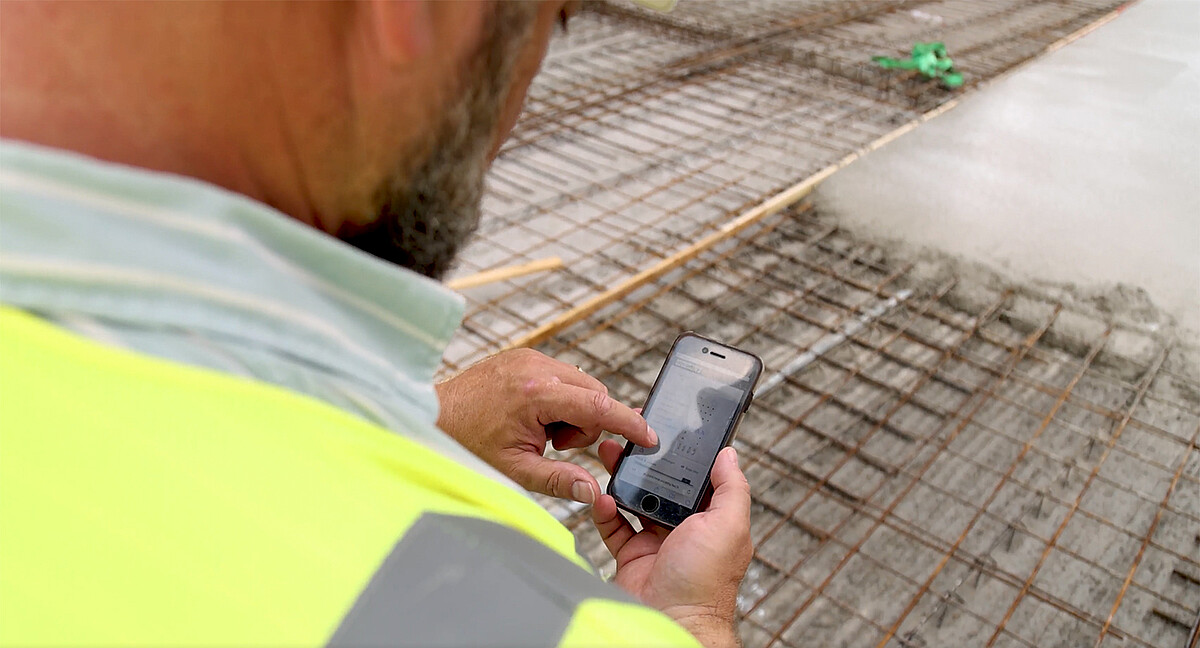
Of course ecoLocked and alcemy are not the only Berlin-based companies pursuing exciting approaches to decarbonizing the world and the economy. Here are a few more:
- NeoCarbon uses waste heat to remove CO2 from exhaust air.
- CarbonOne aims to decarbonize shipping with its technology to produce non-fossil methanol from excess biomass and waste plastic.
- Meloon has developed nanoporous graphene membranes for cost-effective post-combustion carbon capture.
- Carbon Farming produces the “BeyondZero” fuel with a positive CO2 balance.
- Shit2Power produces electricity and green hydrogen from sewage sludge.
Text: Olaf Bryan Wielk, ideenmanufaktur
Header image: © ecoLocked